A Step-by-Step Guide to Backpack Manufacturing
- The Idea Lab
- 3 minutes ago
- 4 min read
Backpacks are more than just bags; they are essential companions for travelers, students, and adventurers. In recent years, the backpack manufacturing industry has experienced significant growth, driven by the increasing demand for quality and functionality. This guide will walk you through the entire process of backpack manufacturing, from understanding the raw materials to the final product.
Backpack Manufacturing Process
The manufacturing of backpacks is a detailed process that combines art, engineering, and creativity. It begins with careful planning and design. Designers sketch various styles and functionalities they want the backpack to have. They consider features like pockets, straps, and zippers, all while keeping ergonomics and aesthetics in mind.
Once a design is ready, the next step is creating prototypes. These mock-ups help manufacturers evaluate the design's feasibility and make adjustments before mass production. Prototypes are crucial in ensuring that the final product meets customer needs.

Understanding the Raw Material of Backpack
One of the most critical aspects of backpack manufacturing is choosing the right materials. Backpacks can be made from various materials, with each having its characteristics and benefits.
Fabric: The most common fabrics used in backpack manufacturing are nylon and polyester. Nylon is durable and resistant to wear and tear, while polyester is often more water-resistant and lighter.
Webbing: This strong fabric is used for straps and handles. It helps provide stability and support to the backpack.
Zippers and Buckles: High-quality zippers and buckles enhance the functionality of a backpack. Manufacturers often opt for YKK zippers known for their durability.
Padding and Foam: These materials are essential for comfort, especially in shoulder straps and back panels. Good padding reduces fatigue and increases user comfort.
Knowing what raw materials are used in backpack manufacturing can significantly impact the quality and ergonomics of the final product.
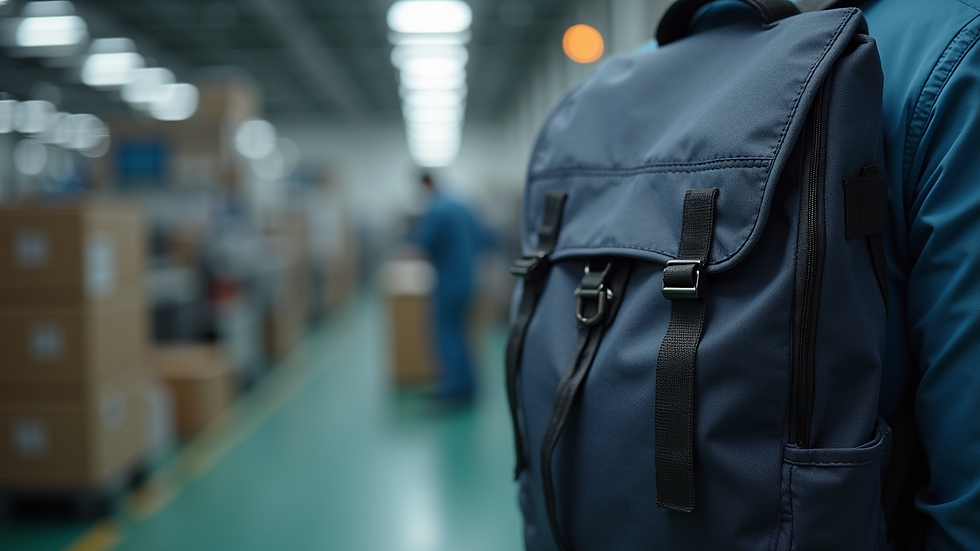
Design and Prototyping
Once the best materials have been selected, it's time to focus on the design and prototyping stages. This phase is crucial to ensure that the backpack will be both functional and appealing to consumers.
Designers create detailed Tech Packs for manufacturers, which include specifications on materials, dimensions, colors, and any other pertinent details. These documents help manufacturers understand precisely what is needed, minimizing errors during production.
Prototyping usually involves creating a small batch of backpacks based on the Tech Packs. This initial run allows manufacturers to test the backpack for quality, durability, and user comfort. Feedback from initial users is essential during this phase to make any necessary adjustments before full-scale production begins.

Manufacturing Techniques
Backpack manufacturing employs a variety of techniques, depending on the design and materials used. Here are some common methods:
Cutting: The selected fabric is laid out and cut into the necessary shapes and sizes according to the design specifications. This step requires precision for accurate dimensions.
Sewing: After cutting, the pieces are sewn together. Advanced sewing machines are often used to ensure neat seams that can withstand stress.
Assembly: This is where different components like zippers, straps, and buckles are attached to the main body of the backpack. Quality control is imperative at this stage to ensure everything is secured correctly.
Finishing Touches: The last step involves checking for any loose threads, cleaning the backpacks, and preparing them for packaging. This quality check ensures that every backpack meets the highest standards before reaching consumers.
Understanding these manufacturing techniques provides insight into the complexity behind how are backpacks made.
Quality Control and Testing
Quality control is vital in any manufacturing process, and backpack production is no exception. After production, each backpack undergoes a rigorous quality check. Inspectors look for faults such as defective zippers, uneven stitching, and durability issues.
Additionally, backpacks are subjected to various tests. These tests may include:
Stress Tests: To assess how much weight the backpack can hold without damage.
Water Resistance Tests: To determine how effectively the backpack can keep contents dry during rain.
User Testing: Feedback from actual users helps identify comfort levels and any needed adjustments.
Ensuring quality at every stage guarantees that the finished product will meet customer expectations.
Marketing and Distribution
Once the backpacks are produced and quality-checked, the next stage is marketing and distribution. Effective marketing strategies are critical for attracting potential customers. Consider the following strategies:
Social Media: Engaging with customers on platforms like Instagram and Facebook can showcase new designs and promotions.
Collaborations: Partnering with influencers or outdoor organizations can increase brand visibility.
Retail Partnerships: Establishing relationships with retail stores can help reach a broader audience.
Distribution also plays a vital role. Backpacks can be sold through various channels, including online stores, retail outlets, and trade shows. An efficient distribution strategy ensures that consumers can easily purchase the backpacks.
The Future of Backpack Manufacturing
As the outdoor and travel industries grow, so does the demand for innovative, high-quality backpacks. Sustainable manufacturing practices are also becoming more prominent, with many companies focusing on eco-friendly materials and processes.
Technological advancements, such as incorporating smart technology into backpacks (e.g., built-in chargers), will likely shape future designs. Manufacturers who adapt to changing market demands will thrive in the evolving landscape of backpack production.
In conclusion, backpack manufacturing is a multifaceted process that requires attention to detail, quality materials, and effective marketing strategies. Understanding each stage allows both manufacturers and consumers to appreciate the craftsmanship that goes into creating these essential products. By exploring the ins and outs of this industry, we can better understand the art and science behind backpack manufacturing.
Comments