How Backpacks Are Made: Unveiling the Global Supply Chain
- The Idea Lab
- Jun 10, 2024
- 5 min read
Updated: Oct 22, 2024
---------------------
In manufacturing, many turn to Alibaba for quotes without proper knowledge, leading to unpredictable pricing.
Just like buying a house or car, starting a garment business requires thorough research.
With 15 years of experience, we offer the expertise you need to confidently take your brand forward. Contact us to get started!
Or head over to our page on Backpacks to learn more about how it all works.
----------------------
Alright, let’s get down to brass tacks and talk about something that impacts millions of lives every day: backpacks. Whether you’re a student, a hiker, or just someone lugging around a laptop and some snacks, backpacks are ubiquitous. But have you ever stopped to think about how these every items day items come into being? It’s time to dive into the global supply chain of backpack manufacturing and uncover the journey from raw materials to the finished product slung over your shoulder.
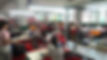
Raw Materials: The Backbone of Backpack Manufacturing
The journey begins with raw materials. Most backpacks are made from a combination of synthetic fabrics like nylon and polyester, as well as zippers, buckles, and padding materials. The production of these materials often starts in countries like China, India, and Vietnam, which are major players in the global textile industry.
Nylon and polyester fibers are produced through a chemical process involving petroleum byproducts. These fibers are then woven into fabric, dyed, and treated for various properties like water resistance or UV protection. Zippers and buckles, often made from plastic or metal, are manufactured in specialized factories. Foam padding is another critical component, providing comfort and support, especially in hiking and travel backpacks.
Fabric Production and Treatment
The fabric production phase is where things start to get interesting. The raw nylon or polyester fibers are sent to textile mills, primarily located in China and India. Here, they are woven into durable fabrics that form the backbone of a backpack’s structure. These fabrics undergo various treatments to enhance their functionality—think waterproof coatings, anti-abrasion treatments, and even antimicrobial finishes to keep things fresh.
Environmental concerns are increasingly at the forefront of fabric production. Manufacturers are adopting more sustainable practices, like using recycled polyester made from plastic bottles. This not only reduces the environmental footprint but also taps into a growing market of eco-conscious consumers.
Component Manufacturing: Zippers, Buckles, and More
Next up, we have the components. Zippers, buckles, straps, and padding might seem like minor details, but they’re crucial for functionality and durability. These components are often produced in specialized factories across Asia, particularly in China and Taiwan.
YKK, a Japanese company with factories worldwide, is one of the largest zipper manufacturers globally. They provide zippers to countless backpack brands, ensuring a standard of quality that’s essential for consumer trust. Buckles and other hardware often come from dedicated manufacturers who focus on creating components that can withstand the rigors of daily use and extreme conditions.
Assembly: Bringing It All Together
The assembly phase is where the magic happens. Factories in countries like China, Vietnam, and Bangladesh take all these individual components and stitch them together into the backpacks we know and love. This stage involves cutting the fabric according to specific patterns, sewing the pieces together, attaching zippers and buckles, and adding padding and straps.
These factories range from large-scale operations producing millions of backpacks annually to smaller, specialized workshops crafting high-end or custom backpacks. The assembly process is labor-intensive, relying on skilled workers to ensure each backpack meets stringent quality standards.
Quality Control: Ensuring Durability and Performance
Quality control is a critical step in the manufacturing process. Backpacks are subjected to various tests to ensure they can withstand the wear and tear of daily use. This includes stress tests on straps and seams, waterproof tests for treated fabrics, and durability tests for zippers and buckles.
Factories often have dedicated quality control teams who inspect each batch of backpacks before they’re shipped out. Any defects are addressed, and only the best products make it to the next stage. This rigorous quality control process helps maintain brand reputation and customer satisfaction.
Distribution and Logistics: The Journey to Retail
Once the backpacks are assembled and pass quality control, they’re packed and prepared for shipment. This phase involves complex logistics, as backpacks are distributed to retailers worldwide. Shipping typically involves a combination of sea, air, and land transport, depending on the destination and urgency.
Backpacks manufactured in Asia often travel long distances to reach markets in North America, Europe, and other parts of the world. Efficient logistics are crucial to ensure timely delivery and manage costs. This includes everything from coordinating shipments to navigating customs regulations in different countries.
Retail and Consumer Purchase
Finally, the backpacks arrive at retail stores or online warehouses, ready for consumers. Retailers range from large chain stores to specialized outdoor gear shops and e-commerce platforms like Amazon. Marketing strategies, including advertising, influencer partnerships, and customer reviews, play a significant role in driving sales.
Consumers today have a plethora of choices, from budget-friendly options to high-end brands. The decision-making process often involves considering factors like brand reputation, product features, price, and sustainability. Brands that offer innovative designs, high quality, and eco-friendly options tend to stand out in a crowded market.
Sustainability and Ethical Considerations
In recent years, there has been a growing focus on sustainability and ethical manufacturing practices. Consumers are increasingly demanding transparency about where and how their products are made.
This has led many backpack manufacturers to adopt more sustainable practices, such as using recycled materials, reducing waste, and ensuring fair labor practices.
Brands like Patagonia and The North Face have set industry standards by prioritizing environmental and social responsibility. They source materials sustainably, implement ethical labor practices, and even offer repair services to extend the life of their products. This shift towards sustainability is not only good for the planet but also resonates with a growing segment of conscious consumers.
Innovation and Future Trends
The backpack industry is continually evolving, driven by advancements in technology and changing consumer preferences. Some of the latest innovations include smart backpacks with built-in chargers and tracking devices, ergonomic designs for better weight distribution, and modular systems that allow users to customize their backpack for different activities.
Looking ahead, we can expect to see even more emphasis on sustainability, with brands exploring new materials like biodegradable fabrics and further reducing their carbon footprint. Additionally, the integration of technology will likely continue, offering consumers more convenience and functionality.
Conclusion
The global supply chain of backpack manufacturing is a complex and fascinating journey. It involves multiple stages, from sourcing raw materials to producing fabrics and components, assembling the backpacks, ensuring quality, and navigating logistics to reach consumers worldwide. Each step is crucial in delivering the durable, functional, and stylish backpacks that millions of people rely on every day.
As the industry continues to innovate and prioritize sustainability, the future of backpack manufacturing looks promising. So, the next time you grab your backpack, take a moment to appreciate the intricate process that brought it to life. Behind every stitch, zipper, and strap lies a story of global collaboration, technological advancement, and a commitment to quality. And that, my friends, is the true essence of the modern backpack.